CNC Machining Lathe Machine Parts: A Pillar of Precision Engineering
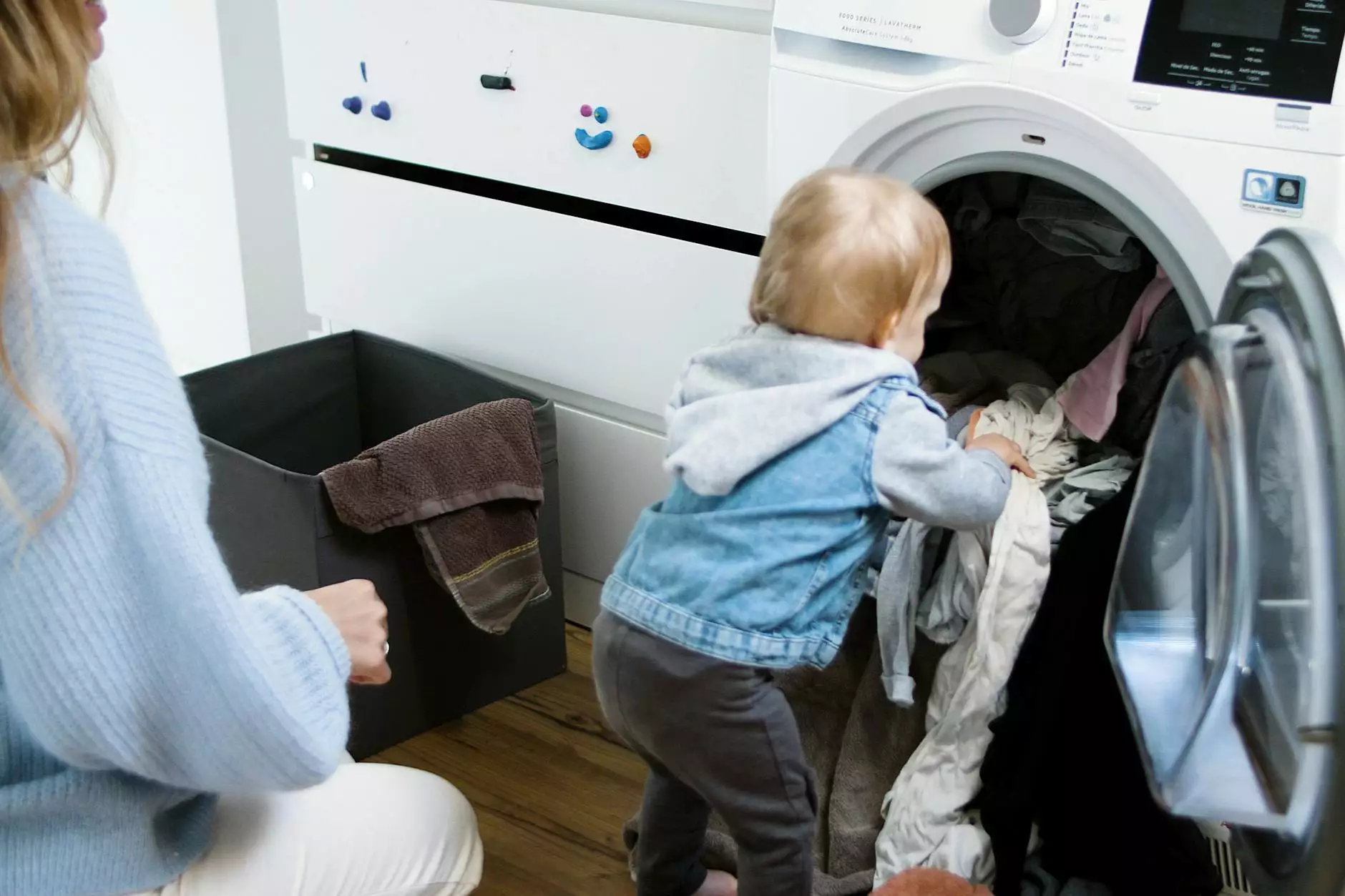
In the realm of metal fabrication, the engineering world continues to evolve rapidly. Among the myriad of tools and machines that define modern manufacturing, the lathe machine holds a place of honor. Particularly, when it comes to producing CNC machining lathe machine parts, the intricacy and sophistication involved cannot be overstated. This article delves deep into the significance, applications, and benefits of these crucial components in the manufacturing industry, particularly as offered by Deep Mould.
Understanding CNC Machining
Computer Numerical Control (CNC) machining has transformed the way components are manufactured. By employing computer software to control machine tools, it allows for unparalleled precision and efficiency. But what exactly is a CNC machining lathe machine? It is a sophisticated device used to shape and cut materials through rotation and multiple cutting tools.
The Role of Lathe Machines in Manufacturing
Lathe machines are vital in the production of various components across several industries. The process involves materials being held securely in a rotating spindle, while cutting tools remove material to achieve desired shapes and finishes. This ability means that lathe machines can produce:
- Cylindrical objects such as shafts and pins
- Complex shapes with the help of CNC technology
- Finely finished surfaces suitable for high-precision applications
Benefits of CNC Machining Lathe Machine Parts
Utilizing CNC machining lathe machine parts provides a myriad of advantages. Here are some of the key benefits:
- Precision: CNC machines offer high levels of accuracy, often measuring parts to within a few micrometers.
- Efficiency: Once programmed, CNC machines can operate continuously with minimal human intervention, vastly enhancing productivity.
- Consistency: Each part produced maintains the same specifications, which is crucial for assemblies that require uniformity.
- Complex Geometries: CNC technology allows for the creation of intricate designs that would be difficult or impossible to achieve manually.
- Reduced Waste: CNC machining optimizes material usage, leading to lower costs and a lesser environmental impact.
Applications of CNC Machining Lathe Machine Parts
The versatility of CNC machining lathe machine parts ensures their application across various sectors, including:
- Aerospace: Where precision is critical for safety and performance.
- Automotive: For manufacturing parts that require durability and reliability.
- Medical Devices: Where exact specifications are essential for device functionality and patient safety.
- Industrial Equipment: Supporting the production of a variety of machinery and parts.
Deep Mould's Commitment to Quality
The emphasis on quality cannot be overshadowed when discussing CNC machining lathe machine parts. At Deep Mould, quality control is paramount. The company employs rigorous testing and inspection protocols to guarantee that every part meets the industry standards.
To achieve excellence, Deep Mould utilizes:
- State-of-the-Art CNC Machines: Ensuring precision in every cut.
- Expert Technicians: Skilled in both CNC programming and machining processes.
- Quality Assurance Processes: Including automated inspections and manual testing to verify dimensions and tolerances.
The Process of Manufacturing CNC Machining Lathe Machine Parts
The journey of creating high-quality CNC machining lathe machine parts at Deep Mould consists of several meticulous stages. Understanding this process ensures customers appreciate the craftsmanship behind each part they receive:
1. Design and Prototyping
The initial step involves comprehensive design work, where engineering teams collaborate with clients to develop accurate designs. Prototypes are created using 3D modeling software to visualize the end product before the full manufacturing process begins.
2. Material Selection
Choosing the right material is imperative for ensuring the performance of the machined parts. Deep Mould offers an array of materials including aluminum, steel, and specialized alloys to suit application needs.
3. CNC Machining
With the design and material finalized, CNC machining equipment is set up. The CNC machines are programmed with precision to follow the specified designs and to deliver the required tolerances.
4. Finishing Processes
After the machining is complete, parts undergo various finishing processes such as deburring, polishing, and coating. These enhance the durability and appearance of the final product.
5. Quality Control and Testing
The final stage involves comprehensive quality checks where every part is measure and tested against company and industry standards. Only those parts that pass these stringent tests proceed to packaging and shipping.
Future Trends in CNC Machining
The field of CNC machining continues to advance, with trends emerging that will shape its future. At Deep Mould, we stay ahead of the curve, ready to integrate new technologies and practices:
- Automation: Increasing the use of robotics to minimize manual intervention.
- IoT Integration: Enhancing machine connectivity for real-time monitoring and data collection.
- Advanced Materials: Exploring new materials that offer enhanced performance properties.
- Eco-Friendly Practices: Implementing sustainable manufacturing practices to reduce environmental impact.
Why Choose Deep Mould for Your CNC Machining Needs?
With competition in the metal fabrication industry intensifying daily, choosing the right partner is critical. Here’s why Deep Mould stands out:
- Experience: Years of expertise in producing high-quality machining parts.
- Customization: Ability to create tailored solutions to meet various client needs.
- Customer Service: Dedicated support teams ready to assist at every step.
- Timely Delivery: Commitment to meeting deadlines without compromising quality.
Conclusion
To conclude, CNC machining lathe machine parts are an integral aspect of modern metal fabrication, providing unmatched precision and efficiency. As industries continue to evolve, the demand for these parts will only increase. Deep Mould stands ready to meet this demand with excellence, innovation, and a commitment to quality. Investing in these components is more than just acquiring parts; it's about embracing the future of manufacturing.